Die Casting Explained
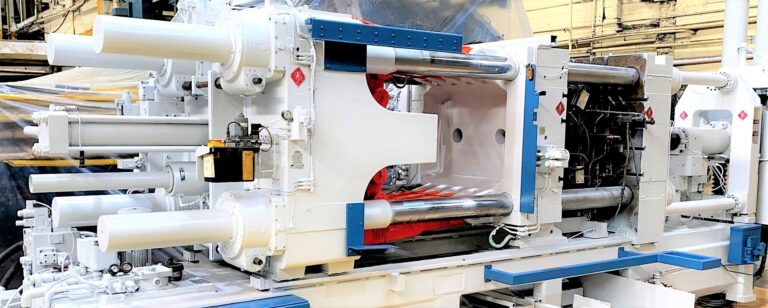
In the die casting process, a mold (called the die) is required. The die is constructed from very high-quality steel specially made for dies. The dies are reusable and are made of two halves. During the process of die casting, molten metal is injected into the closed die under very high pressure through a relatively small hole in one half of the die. When the molten metal has solidified sufficiently, the two parts of the die are opened to expose the actual casting inside. The casting is then removed from the die, cooled further and then finally trimmed. The trimming separates the gates and runners from the casting. The gates and runners are incorporated into the die design as a way to distribute molten metal to the various parts of the die. The trimmed gates and runners are then usually re-melted with new metal also being added. After trimming, further operations can be performed such as drilling and tapping, powder coating and assembly of finished components, etc.
How to Select and Buy a Die Casting Machine
There are many things to take under consideration when buying a die casting machine. This section has been designed to simplify the process of sifting through all the options and selecting the right machine for your needs.
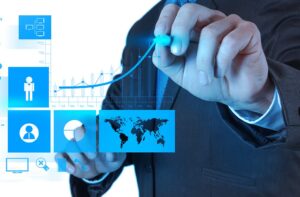
New or SecondHand?
This is the age-old question that most people have. However, most people do not realize that when it comes to die casting machines (as with many other products), manufacturers of these machines produce several “export versions” depending on which “region” of the world they will be sold to. For example, die casting machines produced for the North American market will vary greatly in the quality of materials and technical capabilities when compared to machines produced for “developing” countries. The reality of the matter is that the North American market is much more “mature” and generally speaking has much greater requirements and expectations than other developing markets do. In addition, the level of sophistication, the product technology and budgets for equipment acquisition is greater as well. As such, many die casting machine manufacturers who have been relatively successful in producing machines for developing counties have had almost NO success in developed countries like North America, Europe and other developed markets. In the world market, these machines have become known as “disposable” machines (possibly the term came from disposable shavers). Whereas a machine made in North America or Europe can be rebuilt many times over and over due to superior quality steel, such disposable machines have a very short lifespan of only a few years. After that, it is very hard, if not impossible, to rebuild them properly since the quality of the metal is very poor.